How does Make-to-Stock production planning improve delivery times for plant nurseries?
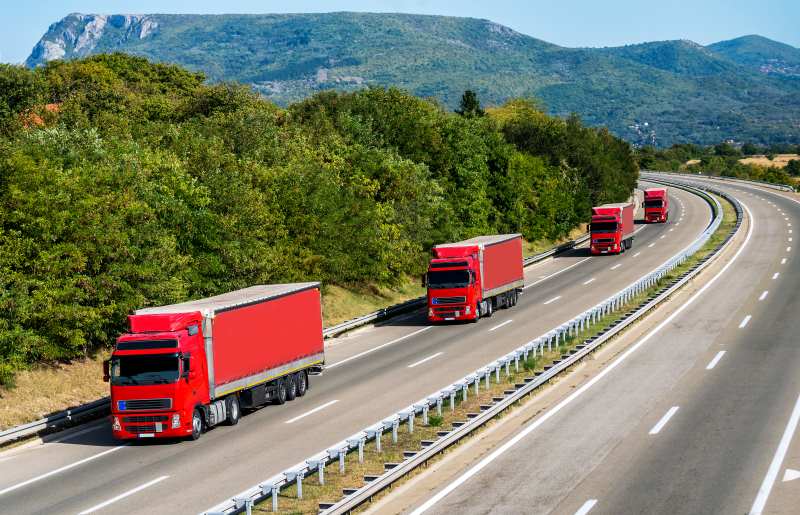
Definition of Make-to-Stock (MTS)
The American Production and Inventory Control Society (APICS) defines Make-to-Stock (MTS) as a production strategy where the producer sells finished goods from stock. This method offers the shortest delivery times, and typically, the customer has minimal direct involvement in the product design.
Characteristics of MTS:
- Short delivery times: Products are readily available for quick delivery.
- Limited customer involvement: Customers do not influence the design of the product.
Application in Software and Challenges
Despite the seeming contradiction of using MTS in sectors like live trading software where products can lose vitality in stock, this strategy is prevalent. The key reason is that the time products spend in stock is usually negligible, making it a viable strategy.
Agriware's Approach to Sales and Production
Agriware users often plan based on expected sales well into the future, though these are not based on confirmed customer orders but rather on Sales Forecasts and Sales Budgets which anticipate future demand.
Detailed Production Planning and Costs
Production managers in Agriware utilize Sales Forecasts to create Production Forecasts, supporting multiple scenarios
Aspects covered in production planning:
- Cost analysis: Users can analyze costs associated with different production scenarios.
- Area usage: Specific cost components like labor, machinery, materials, heating, electricity, and overheads are considered.
- Graphical representation: Scenarios can be visually represented using the Business Intelligence tool integrated into Agriware.
Forward and Backward Scheduling Techniques
Forward Scheduling:
- Starts with receipt of expected orders: Material purchases and activity planning begin upon receiving expected orders to build up stock.
- Determines first possible delivery date: This technique calculates when the product can first be delivered.
Backward Scheduling:
- Based on delivery date: Activities are planned backward from the delivery date, similar to Materials Requirements Planning (MRP) systems.
- Ensures timely delivery: This method determines when production should commence to meet delivery schedules.
Despite assumptions, backward planning is not exclusive to Make-to-Order environments, nor is forward planning solely for Make-to-Stock scenarios. For instance, bedding plant breeders often use backward planning based on Production Forecasts from Sales Forecasts to ensure timely availability for sales.
Customer Order Decoupling Point (CODP)
In production, it's crucial to identify the point (CODP) where the customer begins to influence the outcome of the product. In Make-to-Stock, this point is when the product starts being customized according to customer specifications.
Variability in Production Outcomes
In certain cases, the final product's characteristics may not be predetermined. For example, a Phalaenopsis grower may not know the number of branches a plant will grow or the flowers each branch will produce. Agriware supports planning with multiple sorting, allowing planning per sorting moment and anticipating outcomes per sort.
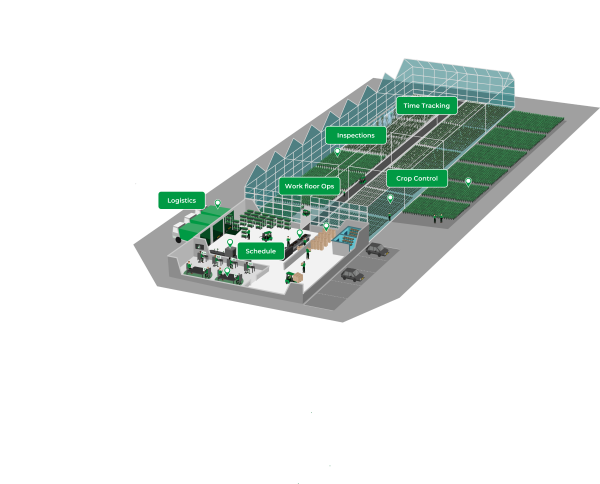
Agriware 365 – Meet Customer Demand with advanced Production Software
Agriware's integrated approach to managing production and sales forecasts, coupled with advanced planning tools, equips horticultural businesses to efficiently manage production and meet customer demands effectively. If you are interested in learning more about these capabilities, please contact us for a demo.
Connect with us
& explore what's possible
120+
#1 Software
20+ Years
Related Articles
%20small.jpg)
What do Growers need for effective Inventory Management?
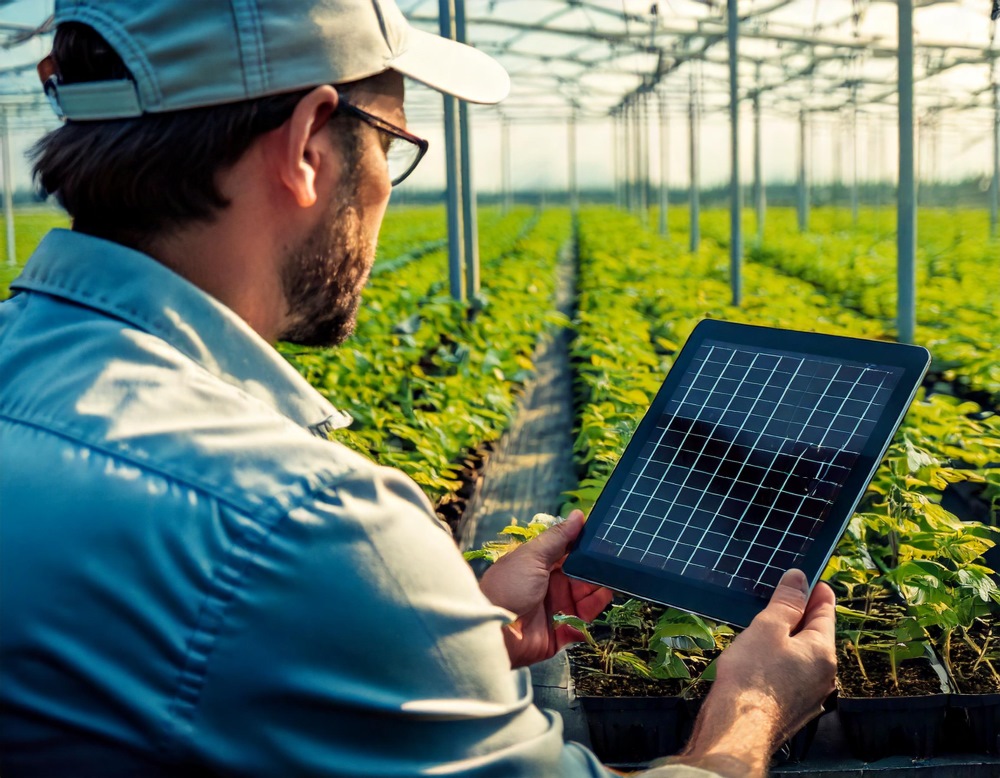
12 Key Software Capabilities to Master Berry Plant Propagation Peaks
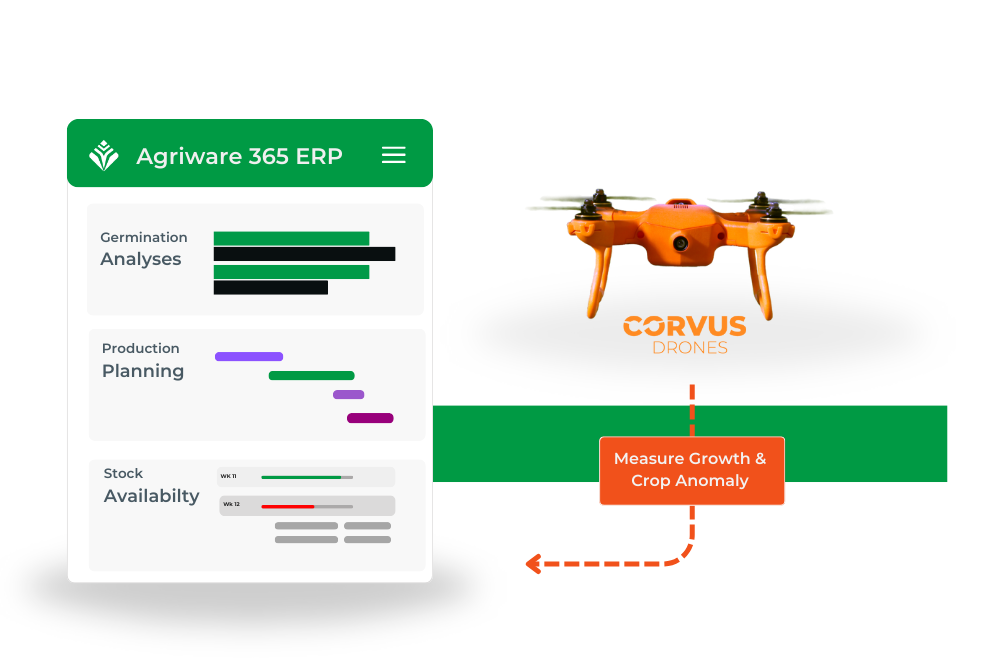